Saturday, May 26, 2012
Sunday, May 20, 2012
Top Three Reasons the Radiography Job Market will Bounce Back
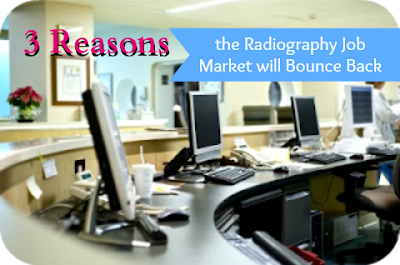
It’s no secret that being a Radiologic Technologist has been difficult in many parts of the country due to fewer available positions. Everyone is bracing for the impact of health care reform and cuts in Medicare reimbursement, which will soon be awarded by the Government at a percentage based on patient satisfaction. For the first time in history, the labor budget will be forced to depend on good service. These issues have caused many hospitals to initiate patient satisfaction campaigns, and to start cutting budgets. With the number one expense for any health care institution being labor, the jobs just aren’t plentiful right now. I address in more detail in my book Becoming a Radiologic Technologist, this should change dramatically within the next 3-5 years:
As I have explained in a prior post (see related posts below), the Baby Boomer generation makes up the largest percentage of the work force in the United States. As of 2011, they have begun entering the retirement age range. We have seen a delay in this due to problems with conventional retirement savings plans being affected by the current depression in the economy. People simply just can’t afford to retire yet, no matter how much they want to. Eventually, the market pendulum will swing the opposite direction as it has consistently done for many decades.
Click Here to Learn How to Land a Health Care Job Fast! (AD)As the largest population in our work force retires, it will create two needs. The first need I will deem the Characteristic Effect on Employment (if you’re a student and haven’t studied this yet, it will make sense soon). First, as the Boomers retire, their current roles will need to be filled with experienced up-and-coming professionals (ejection of the k-shell electron). I anticipate a lot of these positions to be at the supervisory or managerial level (close to the nucleus – a lot of binding energy) due to the amount of time they have spent in the work force. The vacancies created by people filling the Boomers’ jobs will need to be filled by new grads and current employees with a few years of experience (filling of the k-shell by valence electrons). Second, our patient population will increase. As the percentage of employees drops, the percentage of in patients in hospitals will rise, creating a demand for nurses and allied health professionals to care for them.
Due to the high cost of keeping patients in hospitals, expect to see more ambulatory care options rising up.
For us Radiographers, outpatient imaging centers and urgent care centers will be hiring left and right. It costs a lot more money in labor and supplies to keep someone in the hospital for a series of tests than to have them performed as outpatient exams, requiring only the labor cost of the person performing the procedure for the amount of time the procedure takes. It would be good business for health care institutions to invest in more outpatient facilities to handle patient procedures that do not really need to be performed as an inpatient in a hospital. This should also help with the over-use of the Emergency Room that is widely experienced across the country fueled by one reason: convenience.
I know it has been tough out there, and I completely understand that getting a job today can be tough, but I truly believe we are on the cusp of change. The Bureau of Labor Statistics has predicted a 28% growth in our fieldbetween 2010 and 2020, but what they could predict is the state of the economy. The data for their predictions have not changed, but the timing has. It will get better soon.
Related Posts: "Are There Too Many Radiography Grads?"
Photo downloaded from http://www.freedigitalphotos.net/
This post contains affiliate links, which means I receive financial compensation if you make a purchase using these links.
This post contains affiliate links, which means I receive financial compensation if you make a purchase using these links.
Friday, May 18, 2012
Attitude is Everything: Lesson Learned
It's easy to complain about things from our past, but it is much harder to remember the positive experiences that we have about any given period in time. I remember having a particularly rough week during my student internship when I was asked to perform yet another Barium Enema. I knew I should have been grateful because many of my classmates were struggling to gain experience with the exams, but I already had my fill and then some. It seemed like I was assigned every single one that walked through the door, and the staff techs would mysteriously disappear about ten minutes before the appointment time for a scheduled BE.
Late one morning, after already completing three Barium Enemas compared to my classmates' two or three chest x-rays, another requisition printed for... you guessed it - a BE! The Lead Tech looked around the room as everyone avoided eye contact with him, and when our eyes met, I knew what was about to come out of his mouth. The words came out in slow-motion, "Jeremy, go ahead and do the last Barium Enema for the day." I tried not to roll my eyes.
My body language must have indicated that I was disappointed anyways because the Lead Tech pulled me into an unoccupied x-ray room and asked what the problem was. At first I said "nothing" and just wanted to be dismissed to get the exam over with. He persisted saying "I need to know what's bothering you before you do this exam." Then I unleashed my frustration telling him how it wasn't fair that I'm the only one doing all the BE's and how I understood that even though I'm a student (I'm pretty certain I used the term "slave labor" somewhere in there), that even the other students weren't being asked to do them. I told him that I felt picked on somehow. For once, someone asked my opinion without any restrictions, so I gave it to him.
He looked at me very calmly and said "If that's how you really feel, I will assign it to someone else, but I was hoping you would do it." I didn't understand why he wanted me to, so I inquired. What he said to me made me feel small. He said "You are really gentle with the patients and take a lot of time to make sure they are comfortable. I really wanted my mother to have the best care possible, but she's uncomfortable with me performing the exam." I shrunk.
He started to leave the room and I stopped him to tell him I would be happy to do the exam. I apologized for the display of frustration that I expressed, and thanked him for the reassurance for the quality of patient care that I attempt to provide. I also assured him that I would take great care of his mother.
I had never felt so awkward, embarrassed, and foolish. After a few hours, I still felt the need to explain that I had never been complimented by anyone on my performance, so I was caught off-guard when he explained the reason behind assigning me all the BE's. We had an understanding from that moment forward and I never questioned his assignment of tasks after that.
It is easy to feel victimized when you are a student, especially if you are not always given positive feedback
and you feel like you're doing the "grunt work." At the end of the day, as students we are there to learn. We practice through repetition to gain expertise in our skill set. I should have viewed this exam as an opportunity to gain experience, and it always helps to receive a little encouragement along the way.
Late one morning, after already completing three Barium Enemas compared to my classmates' two or three chest x-rays, another requisition printed for... you guessed it - a BE! The Lead Tech looked around the room as everyone avoided eye contact with him, and when our eyes met, I knew what was about to come out of his mouth. The words came out in slow-motion, "Jeremy, go ahead and do the last Barium Enema for the day." I tried not to roll my eyes.
My body language must have indicated that I was disappointed anyways because the Lead Tech pulled me into an unoccupied x-ray room and asked what the problem was. At first I said "nothing" and just wanted to be dismissed to get the exam over with. He persisted saying "I need to know what's bothering you before you do this exam." Then I unleashed my frustration telling him how it wasn't fair that I'm the only one doing all the BE's and how I understood that even though I'm a student (I'm pretty certain I used the term "slave labor" somewhere in there), that even the other students weren't being asked to do them. I told him that I felt picked on somehow. For once, someone asked my opinion without any restrictions, so I gave it to him.
He looked at me very calmly and said "If that's how you really feel, I will assign it to someone else, but I was hoping you would do it." I didn't understand why he wanted me to, so I inquired. What he said to me made me feel small. He said "You are really gentle with the patients and take a lot of time to make sure they are comfortable. I really wanted my mother to have the best care possible, but she's uncomfortable with me performing the exam." I shrunk.
He started to leave the room and I stopped him to tell him I would be happy to do the exam. I apologized for the display of frustration that I expressed, and thanked him for the reassurance for the quality of patient care that I attempt to provide. I also assured him that I would take great care of his mother.
I had never felt so awkward, embarrassed, and foolish. After a few hours, I still felt the need to explain that I had never been complimented by anyone on my performance, so I was caught off-guard when he explained the reason behind assigning me all the BE's. We had an understanding from that moment forward and I never questioned his assignment of tasks after that.
It is easy to feel victimized when you are a student, especially if you are not always given positive feedback
and you feel like you're doing the "grunt work." At the end of the day, as students we are there to learn. We practice through repetition to gain expertise in our skill set. I should have viewed this exam as an opportunity to gain experience, and it always helps to receive a little encouragement along the way.
Wednesday, May 16, 2012
Friday, May 11, 2012
Applying Lean Six Sigma in Healthcare – A look At Product Development
Blog author: Helen Titus, Marketing Director, Digital Capture Solutions, Carestream
The pursuit of less waste, reduced variances and cost-effective, quality care is driving lean six sigma projects at healthcare facilities across the globe—you may be involved in your facility’s full-scale six sigma imitative or you may be applying lean principles to simply improve the productivity of your department.
Lean Six Sigma is not unique to providers. It’s impacting the whole healthcare ecosystem, including vendors like Carestream. It is extensively deployed
throughout our manufacturing organization and it is woven into the fabric of everything that happens on the manufacturing floor.
But the same lean principles that are eliminating waste on the shop floor are also being applied at our front-end to help drive innovation in product development—ensuring what hits hospital hallways has been designed through disciplined problem solving to help overcome our customer’s challenges.
One of the key tenets of Lean Six Sigma is analysis based on fact and direct customer input. So during the very early stages of developing the DRX-Revolution, Carestream’s new entry into the DR mobile imaging market, a team of people went on more than 50 site visits where they not only spoke with rad techs but also observed them conducting mobile imaging exams.
These weren’t just Carestream marketing and management people but rather the software, hardware and electrical engineering team that was assigned the task of developing a new way of approaching an old problem. How do we bring the very best image quality to the sickest patients in the hospital (those in the ICU) in a way that is the most efficient and easiest for the technologist? Seeing and hearing first-hand input from the users empowered the designers to find ways to do things better. They even videotaped them during a routine typical day and mapped out their work process.
The engineers took note of the “waste” in the technologist’s workflow and brainstormed ways to design the product that would eliminate these non-value-added steps. Much the same way that Lean is applied to a manufacturing process.
And sometimes, they just listened.
One tech frustrated by the fact that she couldn’t see driving the x-ray mobile system down the hall said, “I wish the column was made out of glass.” The engineer took that input and although making the column out of glass was not practical, designed a collapsible column so when driving the system it simply just goes away and the tech has a clear driving view. The result of applying the Lean principles is a truly innovative product in a market space where no one thought any further innovation could occur.
Applying Lean Six Sigma methodology is a commitment no matter where it’s deployed—from the hospital to the factory to product development labs. But ultimately applying the principles across the healthcare sphere allows us to work smarter, not harder—and provide more efficient higher quality care.
Are you involved in an LSS project? I’d love to hear your experience.
Wednesday, May 9, 2012
Sunday, May 6, 2012
Becoming an X-Ray Tech
Coming Soon... a new resource for those interested in pursuing a career as a Radiologic Technologist.
UPDATE: For more information on the updated title, "Becoming a Radiologic Technologist", visit my link on Amazon.com (Prime members may borrow this book for free)
Wednesday, May 2, 2012
10 "Do's" and 10 "Don'ts" When it's Slow
When staff techs and students aren't performing their primary function of taking x-rays, they sometimes struggle coming up with ideas of things to do to remain productive. You might be at a clinical site that rarely slows down long enough for you to get in trouble, but sooner or later, you will run into one of those low-volume days. I'm not trying to say that you shouldn't take an opportunity to relax once in a while, but sooner or later, something will need to be accomplished with all the people standing around or people will probably be sent home.
What you decide to do with this time could make a big difference when it comes time to offer a student a job, or during annual evaluations as a technologist. Here are 10 things that you can do in these moments:
What you decide to do with this time could make a big difference when it comes time to offer a student a job, or during annual evaluations as a technologist. Here are 10 things that you can do in these moments:
- Clean and disinfect rooms, wipe down x-ray equipment, portables and c-arms
- Stock linens and supplies (this will help you get used to where the supplies are located)
- Organize equipment and supplies to look presentable
- Check supplies and medications/contrast media for expiration dates and purge expired items
- Check the crash carts and blanket warmers
- Look for depleted oxygen tanks in the department and replace
- Clean image plates if you have CR systems (have a tech show you how if you haven't done it before)
- Make sure each room has oxygen and suction supplies ready to use
- Make copies of any forms that are running low and check to see if printers need paper
- Review images for quality control and practice critique
- Sit down and kick your feet up (and expect a break in 20 minutes)
- Make a personal phone call in the department
- Disappear without saying anything - let someone know if you need to step out
- Engage in gossip
- Complain about being slow
- Have sensitive/personal conversations in common areas
- Play video games on your smart phone or browse social media
- Bring food into the patient care area
- Barge into a room with an exam underway - even if you're just trying to help
- Put KY jelly in another tech's 7-layer burrito and expect them to laugh (true story - wasn't me)
Subscribe to:
Posts (Atom)
Here's a Quick Way to Speed Up Your Xray Exams
Beginning your clinical rotation in x-ray school can be overwhelming. Not only are you plunged into a new environment, you are expected ...

-
I just received a comment on the "In the News" post asking about the accuracy of the preliminary results that the ARRT is going to...
-
One of the more difficult topics for first year students is the correlation between kV and density. Once you think you have this concept do...
-
Unless you work in a hospital that routinely treats pediatrics or you have been around the world of radiography for a while, you may not hav...